ここから本文です。
AGV(無人搬送車)とは何か?基本知識や導入のポイント、成功事例を紹介
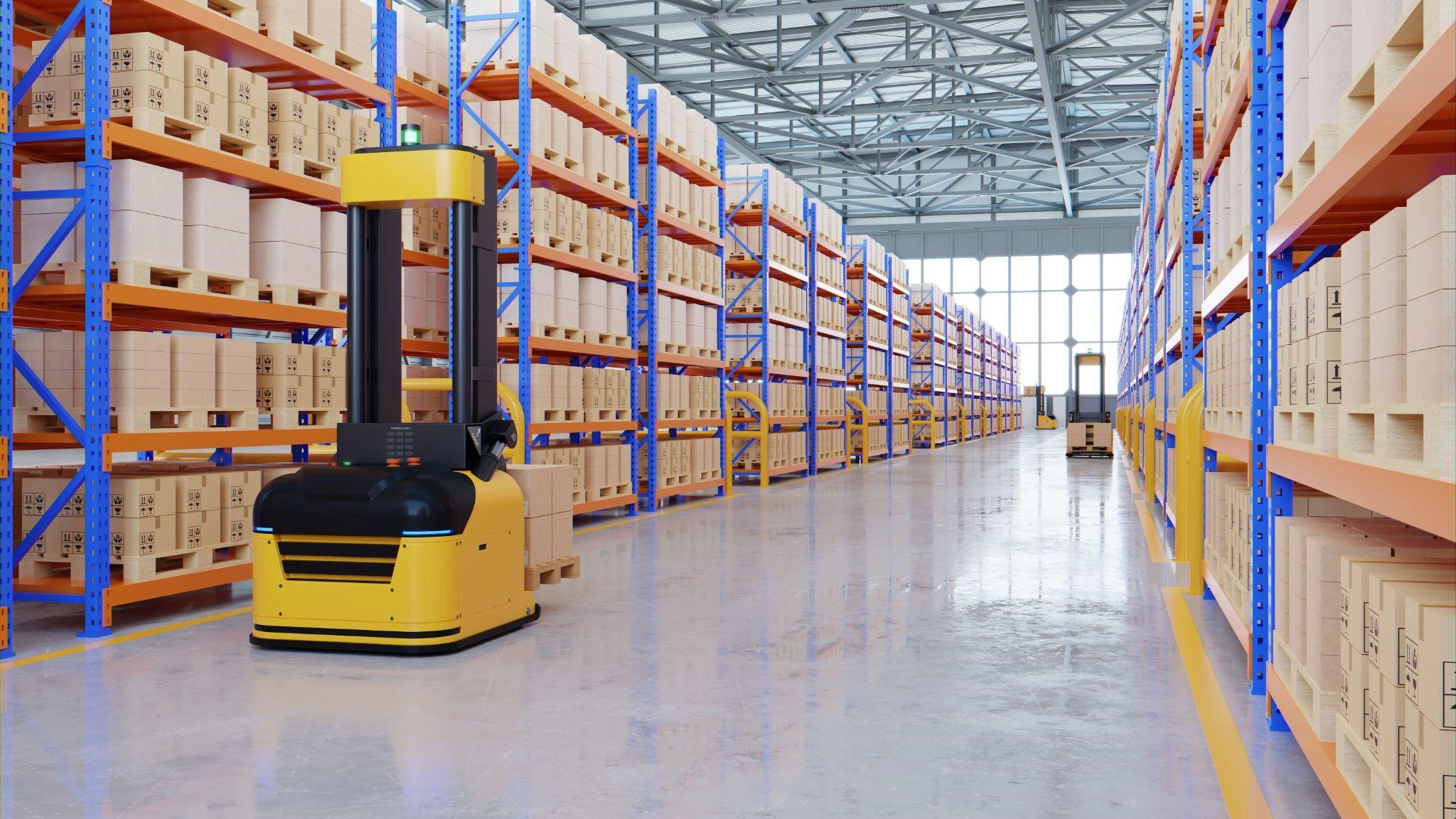
スイッチングハブをはじめとしたネットワークシステム、入退室管理システム、カメラシステム構築に関するお問い合わせはこちら
AGV(無人搬送車)とは何か?
日本では生産性の向上や省人化を目指し、古くからさまざまな種類のロボットが工場などの生産現場に導入されてきました。
自動車産業を中心にその導入が進み「ロボット大国」とまで称される時期もありました。
現在は自動車分野に限らず、電子・電気業界や食品業界などさまざまな領域にその利用が広がっています。
産業用ロボットといえば、多関節のアーム型ロボットが生産ラインで活躍しているイメージが一般的ですが、仕分けや運搬などさまざまな用途でロボットが活躍しています。
その中でも、工場や倉庫での物資や資材の移動にはAGV(無人搬送車)が活用されています。
AGVとは「Automatic Guided Vehicle」のことであり、簡単にいえば「自動誘導車」という意味になります。
その歴史は古く、1980年初頭から物流業界で活用され始めました。
工場内では原料や部品、完成品の運搬などにAGVが活躍しており、以前は磁気テープに従って定められた経路を走行するのが一般的でした。
しかし最新の技術により、AIやセンサー、カメラを駆使して位置を検知し、柔軟に経路を決定できるAGVも登場しています。
これにより、より自由度が高く臨機応変な対応が可能となりました。
AGVには自動運転機能やナビゲーション機能、運搬機能などが備わっており、物流作業の自動化に特化した機能を持っています。
AGVの導入により、作業者の負担軽減やピッキングミスの減少、効率化に伴うコスト削減などの利点が期待できます。
AGVとAMRとの違い
AGVとAMRの違いは、ナビゲーションシステムと柔軟性にあります。
AGVは予め設定された経路に従って進む単純なナビゲーションシステムを使用しているため、変化の少ない状況、例えば安定した環境下で効果的です。
初期セットアップが容易であり、メンテナンスも比較的容易でコストが低いため、反復的な作業に最適です。
AMRは環境をリアルタイムで感知し、障害物を回避できる能力があります。環境が頻繁に変わる場所や、予期せぬ障害物が存在する場所での利用が適しています。
特に適しているのは、何度も交差する場所や、レイアウトが頻繁に変更される倉庫などでの作業です。
AGVは低コストかつ安定した環境での繰り返し作業に向いていますが、AMRはコストが高額です。しかし柔軟性と適応性に優れており、環境が頻繁に変化し、障害物がある場所での作業に適しています。
AGVの主な搬送方法
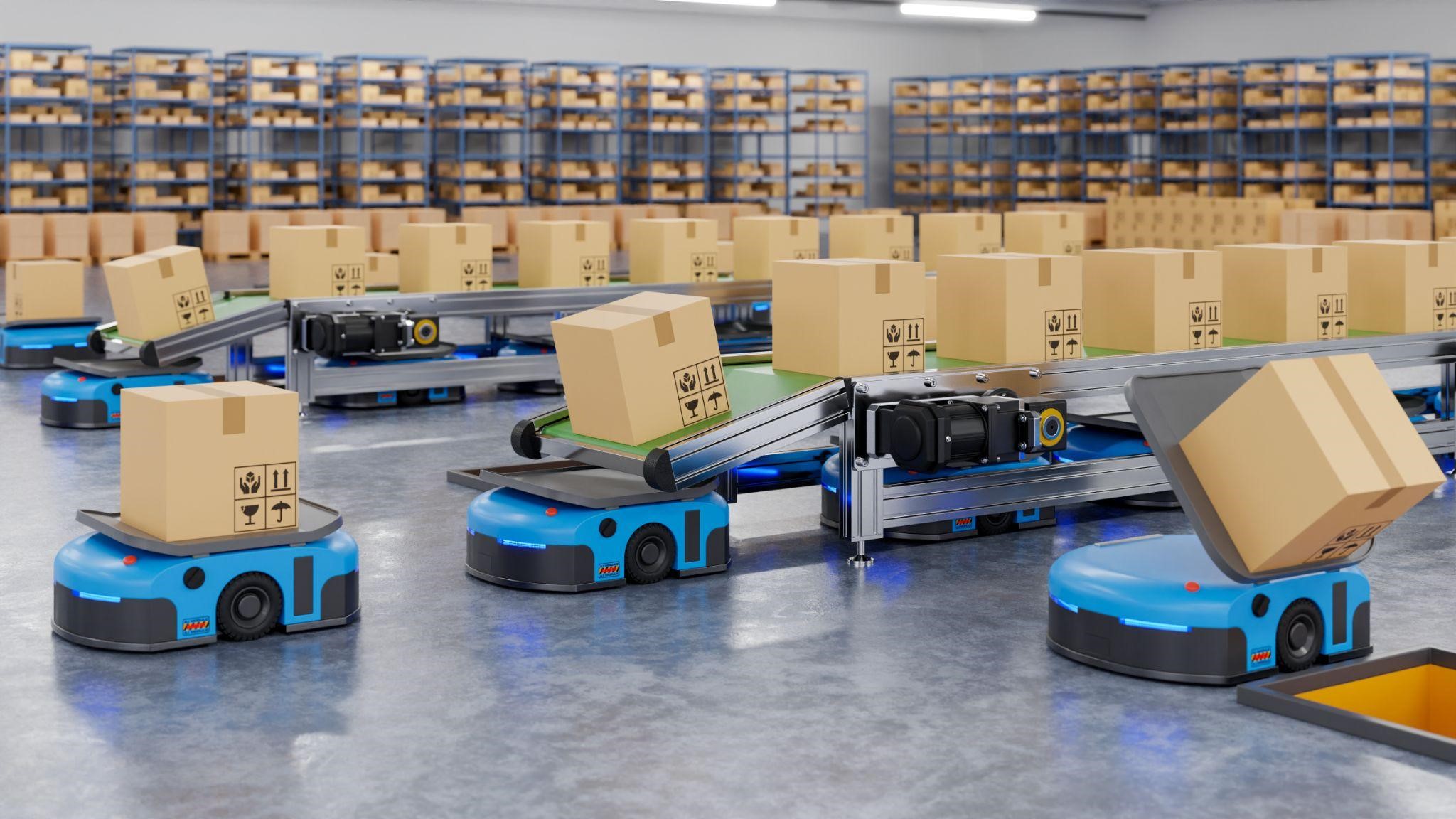
AGVを利用する場合は、適切な機能を持ったAGVを選択する必要があります。
この際に重要となるのは「AGVに何をどのように搬送させるか」です。
以下では、AGVの典型的な搬送方法を紹介いたします。
台車型
台車型とは、手押し台車に似た形状で、台車の上に直接荷物を載せて搬送するAGVの一種です。
従来は人が手動で台車を操作して何度も往復していた作業を、自動で走行する台車型AGVを導入することで、従業員の疲労を軽減しミスを防ぐことができます。
けん引型
AGVは、荷物を直接載せるのではなく、後ろにカゴ台車やパレット台車を連結させ、引っ張って搬送するタイプの搬送車です。
複数のカゴ台車を繋げてけん引する列車のような方法も可能であり、通路が広い場合には一度に多くの荷物を運ぶことができます。
台車型AGVでは数百キロの荷物をけん引しますが、トラクター型AGVでは数トンの荷物をけん引できます。搬送したい荷物の重さに応じて、適切なAGVを選択することができます。
低床型
低床型AGVは、パレットや棚の下に潜り込んでリフトのように荷物を持ち上げて搬送するタイプです。
1台の低床型AGVは、パレットや棚を積んで目的地まで荷降ろしを行う人手不要の搬送が可能です。
これによりAGVの待ち時間が短縮され、効率的な搬送が実現されます。
低床型AGVは持ち上げる機能を持つため、車輪のないパレットや棚を運ぶことができます。
また、けん引装置を取り付けることが難しい台車を搬送する際にも活躍します。
AGVの主な走行方法
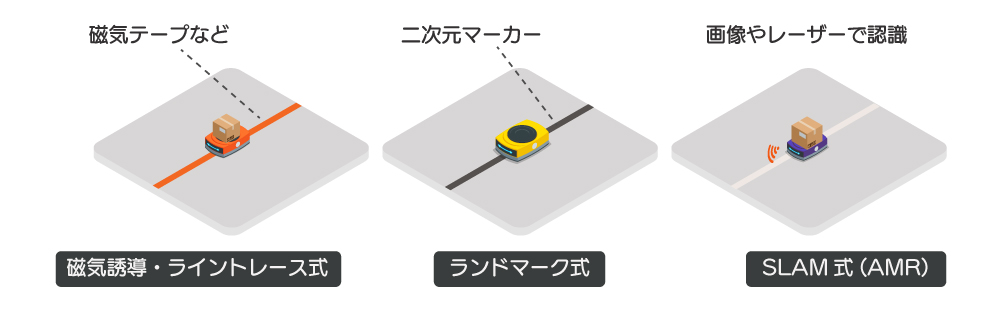
1980年代以来、AGVは工場の生産現場などで広く利用されてきました。
そして、これまでにさまざまな種類の走行方法が開発されています。
走行の精度やルート設置コストの比較は重要ですが、最も重要なのは現場に最適なAGVの走行方法を検討することです。
ここでは、AGVの主要な走行方法についてご紹介します。
磁気誘導・ライントレース式
AGVが走行する経路を指定する方法として、床に磁気テープを敷設し、搭載された磁気センサーによって正確に認識可能な方式があります。
この方式は高い走行直進性と停止精度を誇り、埋め込み方式よりも設置コストが低く、国内で幅広く普及しています。
さらに磁気テープの他にも、光反射テープや電磁誘導ケーブルを使用した方法も存在します。
ランドマーク式
「CarriRo」というZMPのAGV特有の走行方法があります。
この方法は「ランドマーク式」と呼ばれ、地面に配置された二次元マーカーをカメラで認識しながら指示を受け取り、移動する方式です。
従来の磁気テープを使用した誘導とは異なり、要所にのみランドマークを貼ることで、作業員が簡単にルートを確立することが可能となります。
さらにコストのかかる既存の経路の追加や変更も、アプリ上で指示を簡単に変更することで行うことができます。
SLAM式(AMR)
SLAM式は同時位置特定と地図作成を表す言葉であり、ロボットが経路を床に設置しなくても自らの位置を把握しながら進む方法です。
厳密にはAMRに分類されるロボットですが、一般的にはAGVとしても知られています。
ロボットの位置を把握する手法には、「LiDAR SLAM」でレーザー光の反射から距離を測定する方法や、「Visual SLAM」で画像認識技術を応用する方法があります。
床にテープを貼れない現場や棚の配置が頻繁に変わる環境では、SLAM式の採用が一般的です。
またフォークリフトが頻繁に走る環境ではテープがはがれやすいため、誘導体を必要としないSLAM式のAMRが活躍します。
AGVの連携機能
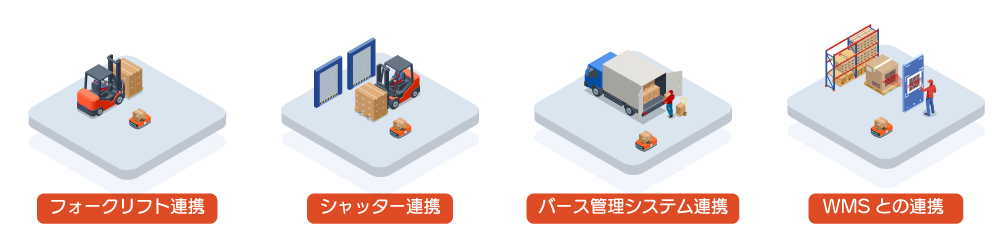
倉庫や工場全体を見ると、搬送のみを無人化しても、荷物の積み降ろしや検品などの作業には人手が必要です。
AGVの選定時には「搬送方法」と「走行方法」に加えて、「連携機能」が重要視されています。
省人化・無人化を実現するためには、搬送にかかわる全ての作業と連携可能なAGVが必要とされています。
ピッキング・フォークリフト連携
AGVによる自動運搬を行う際には、必ず荷物をラックやカートに積む作業が必要です。
この積載作業も自動で行うことで、より効率的な操作が可能となります。
AGVと積載作業の連携には、製造ラインでのピッキングマシン、倉庫内での自動フォークリフトとの連携が考えられます。
さらにAGVが棚まで移動し、人間がピッキング作業を行うGTP(Goods to person)方式の連携手法も存在します。
シャッター・エレベーター連携
無人搬送車にとって搬送作業の経路には、シャッターやセキュリティドア、さらにはエレベーターといった障害物が存在します。
これらの装置と無人搬送車を連携させることで、これまで人が行っていた搬送作業まで無人化することが可能になります。
バース管理システム連携
搬送業務を伴う典型的な場所として、トラックの着発地である荷役場での積み降ろしが行われます。
トラックの着発管理システムとAGVを組み合わせることで、必要なタイミングでAGVが到着し、効率的な搬送業務を実現することが可能となります。
倉庫管理システム(WMS)との連携
倉庫内での物の位置によって、必要な移動作業も異なってきます。
在庫や入出庫の情報をデータで管理する倉庫管理システム(WMS)とAGVを組み合わせることで、適切な経路を設定できるようになります。
AGV導入におけるポイント
ここではAGV導入におけるポイントを解説していきます。
費用対効果
AGVを導入することで、どれほどのコスト削減が可能かを検討することが重要です。
従業員の労働力だけでなく、疲労や注意不足による人為的ミスによる損失なども削減できるコストの一部です。
導入後の隠れたコストも考慮に入れておくと、よりよい判断ができます。
なお、複数台の購入が必要な場合やシステムが含まれると、AGV本体の倍の金額がかかるケースもあります。
1台からリースできるメーカーも存在するため、そうした機会を活用することも検討しましょう。
現場に適した搬送・走行方法
機能が優れていても低コストであっても、実際の現場に適していないAGVは無意味です。
現場が扱う荷物、周囲のロボットや作業環境、そして作業プロセスに応じた外部デバイスといった倉庫や工場の特性を十分に理解し、最も適したAGVを選択することで、導入後の効果をさらに高めることができます。
まずは専門業者に相談する
自社で適切なAGVや機能を選択するのは難しい場合があります。
現場に最適な省人化・無人化ソリューションを提案してもらえますので問い合わせてみましょう。
AGV導入の成功事例
ここではAGV導入の成功事例について紹介していきます。
従来の設備では対応できる重量や距離に制限(課題)
リコーグループの厚木工場では、これまで倉庫から組み立て作業場までの間で部品を運搬する際には、ハンドリフターを使用していました。
この方法では、テーブルの昇降や移動に人力が必要だったため、運べる重量や距離に制限がありました。
さらに荷物が崩れることで、破損や衝突事故が発生する危険性も存在します。
作業時の安全性を確保するため他社製のAGVを導入しましたが、これは磁気誘導式でした。
そのためルート変更時に貼り付ける必要のある磁気テープや工事により、コストや手間がかかることとなりました。
AGVを採用することで時間やコストを削減(解決策・成果)
そこでリコー厚木工場では、課題解決のために光学式技術を採用した無人搬送機M2を導入しました。
光学式の利点は市販の黒ビニールテープを使用することで、磁気テープよりも設置時間を90%、コストを96%削減できる点です。
リコーグループの工場では現在23台のAGTが稼働中であり、部品の無人運搬や移動を行っています。
これにより「無人化製造ライン」の構築を進めています。
まとめ
製造や物流の現場で効率化を図るために注目されている「AGV(無人搬送車)」について、本記事では基本知識や導入のポイント、成功事例などを紹介しました。
AGVは自動走行するロボットであり、物の搬送を人の代わりに行うことができる画期的な技術です。
AGVの導入に際しては、搬送方法や走行方法などを考慮することが重要です。
この記事で紹介したポイントを参考にして、効果的な導入を実現していきましょう。